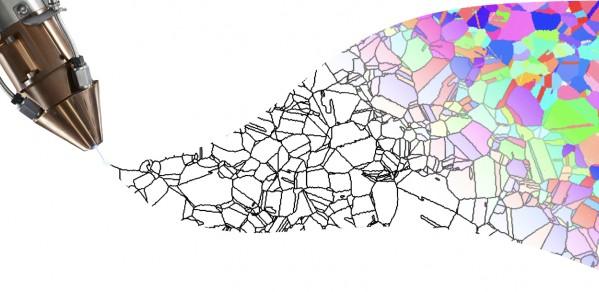
Dr Matteo Seita, Granta Design Assistant Professor has won the 2023 Young Innovator in the Materials Science of Additive Manufacturing Award. He explains how 3D printing technology can be used to enable a lower carbon footprint.
My research focuses on metal 3D printing. The reason why 3D printing technology has gained so much attention in recent years is that it enables the production of parts with improved performance by optimizing their geometry. For instance, metal components can be designed with an open lattice architecture (something that resembles the Eiffel tower) to be both strong and lightweight. This is possible because 3D printed builds are made from the bottom up, by stacking slices of material on top of one another. Conceptually speaking, it is like assembling LEGO bricks into a 3D architecture. No other manufacturing process provides the same freedom to design and produce bulk metal parts with arbitrary shape.
The idea of mixing different microstructures to make materials with superior properties is not new. Blacksmiths have been doing that for thousands of years using complex thermal and mechanical processes to forge microstructure mixtures that impart metal alloys with high strength and toughness. The extraordinary performance of katana swords is an example of this materials design strategy, which yields a steel blade that is both hard and durable.
"Improving the specific strength of materials implies being able to achieve the same load-bearing capabilities using less materials and thus less mass. Light yet strong metals are very important for transportation, where lightweight translates directly into less fuel consumption and thus lower carbon footprint," Dr Matteo Seita, Dept of Engineering
Applying the same principles to 3D printing technology is very challenging (if not impossible) using traditional blacksmithing strategies, since they are not compatible with this “brick-by-brick” manufacturing process. Thus, my research is concerned with devising novel 3D printing processes to gain control over the microstructure of metals and on using them to create new “microstructure architectures” that impart the material with superior properties.
My vision is that this microstructure-based materials design paradigm, combined with the widely celebrated geometric design freedom provided by 3D printing, will be the foundation of sustainable metal manufacturing in the future. Geometry and microstructure-optimized parts could easily last longer and have even higher strength over weight ratio compared to the current 3D printed designs. Longer lifetime equals less replacement of parts and thus less waste of materials and energy. Moreover, improving the specific strength of materials implies being able to achieve the same load-bearing capabilities using less materials and thus less mass. Light yet strong metals are very important for transportation, where lightweight translates directly i
Credit: Dr Matteo Seita